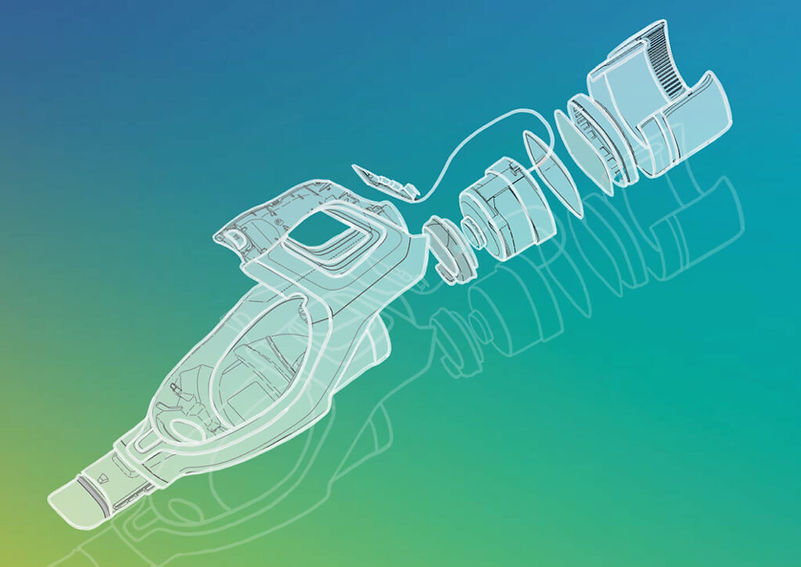
Repairability in consumer electronics
To complete my master at the TU Delft I chose a graduation project in which I could learn more about my favourite subject: physical design that allows for better repair, refurbishment, remanufacturing and recycling. In this project I had the chance to do a graduation internship at Philips Domestic Appliances with the focus on repairability.
​
The goal was to assess the repairability of their current cordless vacuum cleaners and propose strategies to improve. In total six cordless vacuum cleaners were disassembled and mapped using the Disassembly map method (De Fazio, 2019). In our modern world repair often means replacing broken components and thus restoring the original functions of a product. Therefore the level of ease in which a product can be disassembled is important to enhance repairability. Products in which the most important components can be reached quickly and without breaking other parts are in this perspective best repairable.
​
During the period of working on this project the French Repairability Index (FRI), an obligatory label for electronic consumer products in France, was introduced. I had seen earlier what a powerful force legislation could to make sustainable impact when the EC limited Vacuum cleaner wattage to 900W. To help make my assessment more future oriented I adapted the Disassembly map to a version that was more compatible with the FRI
​

​
Hands on disassembling the products was one of my favourite experiences during this project. After getting to know six different designs I got a good feeling for the different types of build up and where to put my spudger to unlock hidden snap fits.
​
Eventhough the FRI is an amazing initiative, as a schooled product designer I have some points of critique. Since new legalisation will also influence future products it is important to consider what kind of design choices it stimulates.
Currently there is a big emphasis on a small amount of disassembly steps. These are the amount of actions that one needs to carry out to obtain important components (priority parts). This subcategory is weighted heavier compared to the topic of re-usability of fasteners. The result of this approach is that a product that has a very low amount of disassembly steps but breaks down during the repair can get a high score. This is problematic since fasteners or components that break need to be replaced. From a consumer perspective this means ordering (sometimes niche) components, financially investing more besides the originally broken component and waiting for the components to arrive. These are all obstacles for enhancing repair and longer use of consumer products.
​
On a second note, the definition of a disassembly step is quite complex. In my personal belief the label would benefit from a simpler approach. The three different types of disassembly steps often confuse engineers which is a particularly undesired effect since they are the ones who give shape to new products.
​

R
Flat lay of one of the 6 assessed products
The three types of disassembly steps as proposed in the French Repairability Index